|
Quick Navigation |
|
Contact Us |
|
B-4/2, Suman CHS, Suman Nagar,
S.T.Road, Chembur,
Mumbai 400 071, INDIA. |
|
 |
91 22 25272863 |
|
 |
admin@pizo.co.in
|
|
Location |
|
Googlemap |
|
|
PIZO- NFK PARTNERSHIP |
 |
Nippon Furnace Co Ltd (NFK), Japan has developed and designs and manufactures and supplies Industrial furnaces and its related technology including High Cycle Regenerative System known as HRS. NFK specializes in niche equipments used in Waste to Energy, Waste Heat Recovery and Waste Treatment. This helps in energy savings, environment friendly and greener applications.
PIZO is representing NFK for Industrial Furnace, Burners, Incinerators, Process Equipment and allied products and services in India.
Nippon Furnace Kogyo started manufacturing and marketing combustion burners soon after World War II, initially under technical licensing agreements with such world famous burner manufacturers as Bloom, Coen, Pillard and Forney. The company later put on sale high quality high efficiency burners developed in its own R&D facilities, and established its position in the combustion technology market. Starting in 1987, the company stepped up its R&D efforts to develop a new Regenerative Combustion System "HRS", High Cycle Regenerative Combustion System, to simultaneously respond to the evolving global environmental consciousness and meet the needs of a rapidly expanding economy. |
|
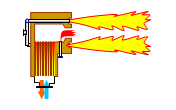 |
High Cycle Regenerative
Combustion System |
|
The HRS Technology was adopted as the core technology in the High Performance Furnace Development Project, one of Japan's national development projects.
Since 1999, the HRS burners have been adopted by many industrial furnaces for the National Field Test Project and have proved their excellence in reducing both fuel consumption (by over 30% compared to conventional burners) and NOx emissions.
NFK's combustion burners and equipment based on the most advanced combustion theory and technical data are now receiving worldwide acclaim for high efficiency and high quality. |
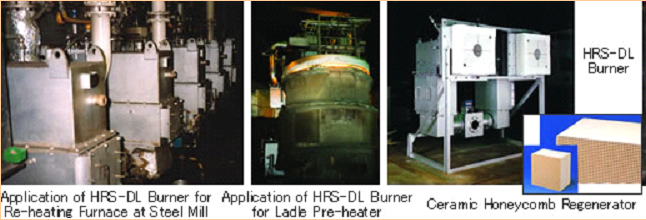 |
APPLICATION OF HRS BURNER for HEAT TREATMENT FURNACE |
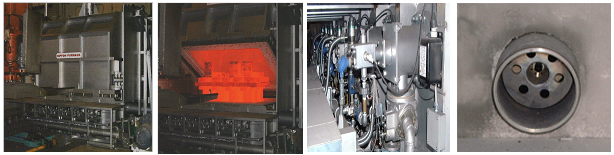 |
|
|
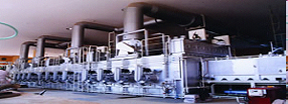 |
Industrial furnaces |
|
Industrial furnace business has also been started at the same time of NFK's establishment together with burners & combustion equipment business. NFK succeeded to develop various kinds of original designed heat treatment furnaces. The typical example of them is so called High Performance Industrial Furnaces which are equipped with regenerative burners incorporating a ceramic honeycomb and this technology has been contributing to environmental protection as CO2 and NOx reduction. Especially the patented regenerative radiant tube furnaces in the middle and high temperature range are unique and competitive designed ones and have been receiving client's satisfaction. |
Heat Treatment Method Category |
Heat Furnace Shape Category |
Heating Method Category |
Normalizing furnace |
Batch type furnace |
Gaseous fuel firing |
Hardening furnace |
Box furnace |
(conventional and regenerative type) |
Tempering furnace |
Car bottom type furnace |
Direct fired burner |
Annealing furnace |
Bell type furnace |
Radiant tube burner |
Baking furnace |
Pit type furnace |
Oil fuel firing |
Solution treatment furnace |
Elevator type furnace |
(conventional and regenerative type) |
Aluminum heat treatment furnace |
Retractable type furnace |
Direct fired burner |
Nonferrous metal annealing furnace |
Continuous type furnace |
Electric resistance heating |
Glass heat treatment furnace |
Roller hearth type furnace |
|
Glass lining furnace |
Tray pusher type furnace |
|
Enameling furnace |
Chain conveyor type furnace |
|
Brazing furnace |
Overhead conveyor type furnace |
|
Bluing furnace |
Rotary type furnace |
|
Atmosphere gas conversion furnace |
Mesh belt conveyor type furnace |
|
|
|
|
|
Incineration Unit. Process Equipment |
Incinerator for Waste Liquids Containing Solid Particles |
Waste liquids containing solid catalyst particles at chemical plants can be thermally cracked by effective contact with the combustion flame of the auxiliary fuel burner of the V-II type vertical incinerator. Combustion gas is quenched in the direct contact type quenching chamber at the bottom and solid materials are recovered by a venturi scrubber.
The incineration and the thermal cracking process are performed effectively using the space and walls of the incinerator. Recovery of solid materials is possible even if the ratio of the solids in the waste liquid is as high as 30%-40%. |
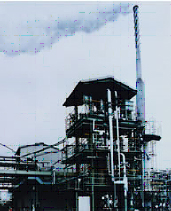 |
Incinerator for Halide Wastes |
NFK has successfully developed a reliable incineration and thermal cracking system. The refractory lining materials of the incinerator are designed in accordance with the specific nature of the halides to be fed into the system.
The combusted waste gas from combustion chamber flows to the scrubbing tower after it is quenched in the quenching chamber at the bottom and scrubbed by the alkaline liquid in the scrubbing tower filled with special packing materials. The concentration of halides in the exhaust gas can fully meet the strict environmental regulations. |
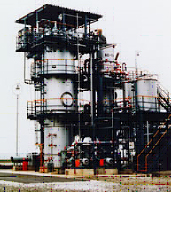 |
Incinerator for Waste Liquids and Waste Gas |
The system consists of a combustion chamber, a quenching chamber. a bag filter and an exhaust stack. In the combustion chamber, waste liquid and/or the gas is incinerated using high temperature auxiliary fuel firing gas. It is then quenched in the quenching chamber.
The quenched gas is fed, and filtered by the bag filter and diffused to the atmosphere from the stack.
|
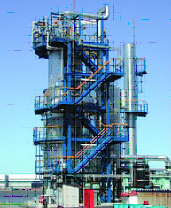 |
Acid Gas Incinerator |
Acid gas which contains H2S, is produced by the desulphurization processes in oil and LNG refining plants. This incinerator oxidizes such toxic gases and hydrocarbons converting into SO2, CO2 and H2O. Either natural draft or forced draft is applicable for this system.
No auxiliary fuel firing is required when the LHV of acid gas is over 3,500kJ/Nm3. |
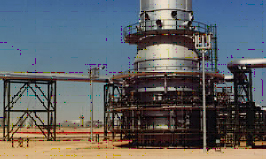 |
Equipment for Waste Plastics Liquefaction Plant |
NFK constructed and supplied a thermal cracking vessel, a residue extracting unit, a reheating furnace and a waste gas (contains) incinerator for their customer plant in Japan. |
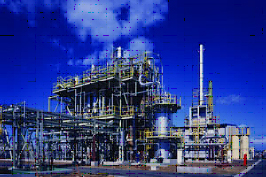 |
Tail Gas Incinerator for Sulphur Recovery Unit |
This incinerator is designed to oxidize sulfur compound (H2s, COS, CS2, Sn) in tail from SRU and/or off gas from TGTU using auxiliary fuel firing. Treating gas is fed through branched lines of the header part to the incinerator. This makes possible the complete mixing of treating gas and high temperature gas produced by combustion of auxiliary fuels. |
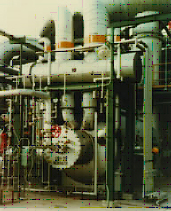 |
Cyclone Melting Furnace for Sewage Slush |
NFK supplied a cyclone melting furnace for sewage sludge for a sewage disposal plant constructed by JGC Corporation |
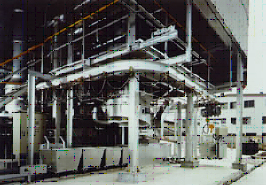 |
|